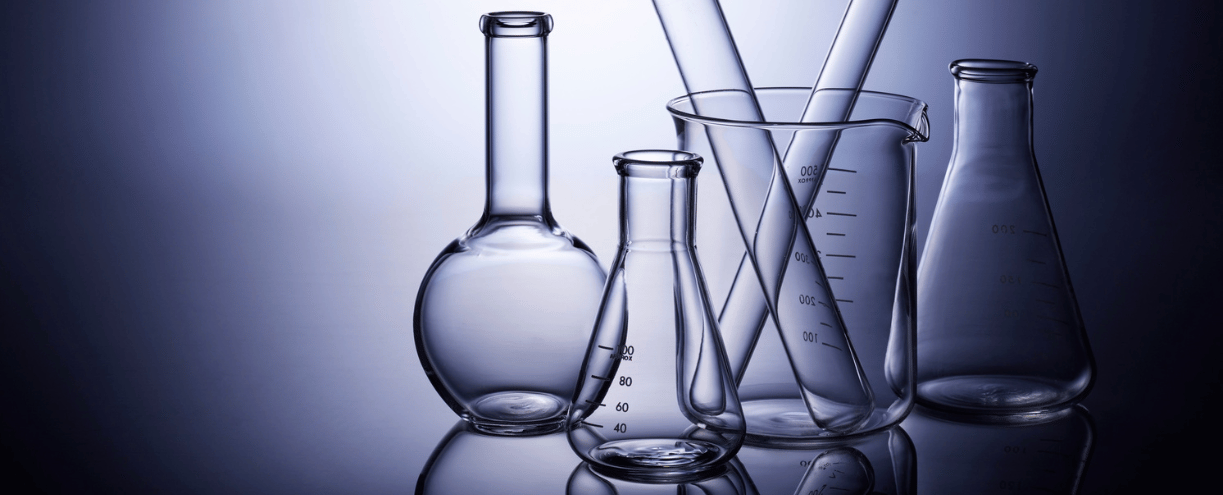
Required Caustic Concentrations
Did you know that that caustic concentration required to effectively CIP stainless steel food processing surfaces is dependent on the following factors?
- Soil Composition
- Processing Temperature
- Level of Mechanical Action/Flow
- Available Time
One of the most important factors to consider is the processing temperature. When food substances are treated with heat, as in cooking or pasteurizing, the heat can change the chemical structure of the food. This process is called denaturization. When a food product is denatured, it becomes much more difficult to remove and will typically require elevated chemical concentrations, cleaning temperatures, increased mechanical action, and more time to effectively remove. They may even require the use of a caustic enhancing additive such as Defoamer No. 553, Enhance No. 567.
By way of comparison, cold or ambient temperature processes will likely require much less chemical concentration, less temperature, less mechanical action, and less time, to produce an effective clean.
cold/ambient processing surface CLEANING PARAMETERS
For cleaning cold/ambient processing surfaces, the typical CIP cleaning parameters are:
- Caustic Chemical Concentration: 0.40 – 0.75 oz/gal of caustic CIP cleaner
- Flow: Minimum of 5 ft/sec through the largest flow path (or meet the minimum CIP flow
- Requirements per the equipment manufacturer’s specifications)
- Temperature: 135 – 150°F
- Time: 5 – 15 minutes.
This would cover such things as cold storage silos and cold or ambient temperature transfer lines.
hEAT tRANSFER EQUIPMENT & sEPARATOR/CLARIFIER Cleaning Parameters
For cleaning equipment such as heat transfer equipment (HTSTs and evaporators) and separators/clarifiers the typical cleaning parameters are:
HTST’s/Pasteurizers
- Caustic Chemical Concentration: 1.0 – 2.0% caustic (as sodium hydroxide)
- Flow: Minimum of 10% higher than process flow or manufacturer’s recommended CIP flow.
- Temperature: 170 – 180°F (10°F hotter than processing temperature)
- Time: 45 – 60 minutes.
Evaporators
- Caustic Chemical Concentration: 1.5 – 4.0% caustic (as sodium hydroxide)
- Flow: Minimum flow would be same as process flow
- Temperature: 160 – 180°F (typically cleaned under vacuum, so CIP temperature would be the same as processing temperature.)
- Time: 45 – 60 minutes.
- Note:
- If cleaning a milk evaporator, the first caustic wash should not exceed 0.75% caustic. Exceeding 0.75% caustic on the first wash could cause the milk protein in the evaporator to turn into an orange rubbery gel, making it much harder to remove. This is known as a Maillard Reaction. The second caustic wash should hit the higher 1.5 – 4.0% caustic concentration.
- Whey protein evaporators do not typically require a milder alkaline pre-wash.
Separators/Clarifiers
- Caustic Chemical Concentration: 0.75 – 1.5% caustic (as sodium hydroxide)
- Flow: Should be maximum stuffing capacity of separator or clarifier
- Temperature: 160 – 180°F
- Time: 45 – 60 minutes.
- Note:
- Even though the separator or clarifier disc stacks spin at a high rate of RPM’s, the CIP of such units is more of a “soak” clean rather than a CIP with turbulent flow.
- The caustic solution serves to soften/loosen/dissolve the soil and the mechanical “shoots” discharge the soil from the disc stack and bowl.
When testing caustic cleaning solutions for cold/ambient temperature processing surfaces, we typically measure the chemical concentrations is oz/gal. This should usually require a titrant use of under 15 drops.
When testing caustic cleaning solutions for high heat equipment and/or separators and clarifiers, we typically measure concentrations in % by weight active caustic. In most applications, the typical titrant use should between 7 - 20 drops. If we titrated the caustic used in high heat equipment in oz/gal, it would require 25 – 75 drops of titrant! Below are conversions of various caustic products and the fluid ounces required to achieve a 1% caustic solution by weight:
Weight per Gallon: 12.73 Fluid Ounces per Gallon for 1% Caustic: 1.71 Weight per Gallon: 12.45 Fluid Ounces per Gallon for 1% Caustic: 1.90 Weight per Gallon: 12.73 Fluid Ounces per Gallon for 1% Caustic: 1.77 Weight per Gallon: 12.15 Fluid Ounces per Gallon for 1% Caustic: 2.30 Weight per Gallon: 11.12 Fluid Ounces per Gallon for 1% Caustic: 3.34 |
Weight per Gallon: 11.37 Fluid Ounces per Gallon for 1% Caustic: 3.27 Weight per Gallon: 11.70 Fluid Ounces per Gallon for 1% Caustic: 2.75 Weight per Gallon: 12.01 Fluid Ounces per Gallon for 1% Caustic: 3.14 Weight per Gallon: 10.95 Fluid Ounces per Gallon for 1% Caustic: 4.75
|
Reach out to the RITE Team™ for more information on caustic concentrations.